A Comprehensive Guide to the Refine and Benefits of Plastic Extrusion
In the huge world of production, plastic extrusion emerges as a necessary and highly effective process. Transmuting raw plastic right into constant profiles, it provides to a myriad of industries with its exceptional convenience.
Recognizing the Fundamentals of Plastic Extrusion
While it might appear facility in the beginning look, the procedure of plastic extrusion is fundamentally easy - plastic extrusion. It is a high-volume manufacturing strategy in which raw plastic is melted and formed right into a continuous account. The process starts with the feeding of plastic product, in the kind of granules, pellets, or powders, into a warmed barrel. The plastic is then melted utilizing a mix of warmth and shear, applied by a revolving screw. When the molten plastic gets to the end of the barrel, it is required via a little opening recognized as a die, forming it into a desired form. The designed plastic is after that cooled, strengthened, and reduced right into wanted sizes, completing the procedure.
The Technical Refine of Plastic Extrusion Explained

Sorts Of Plastic Suitable for Extrusion
The choice of the right type of plastic is an important facet of the extrusion procedure. Various plastics use distinct residential or commercial properties, making them much more matched to specific applications. Understanding these plastic types can considerably enhance the extrusion process.
Contrasting Plastic Extrusion to Various Other Plastic Forming Methods
Recognizing the sorts of plastic suitable for extrusion paves the way for a wider conversation on exactly how plastic extrusion compares to other plastic forming methods. These consist of shot molding, strike molding, and thermoforming. Each approach has its distinct usages and advantages. Injection molding, for example, is excellent for producing intricate parts, while strike molding is excellent for hollow things like bottles. Thermoforming excels at forming superficial or huge parts. Nevertheless, plastic extrusion is exceptional when it comes to creating continual accounts, such as gaskets, seals, and pipes. It additionally enables a regular cross-section along the length of the product. Thus, the selection of approach mostly relies on the end-product demands and specifications.
Key Advantages of Plastic Extrusion in Manufacturing
In the world of production, plastic extrusion offers several substantial advantages. One significant benefit is the browse around this site cost-effectiveness of the process, that makes it a financially appealing manufacturing approach. Additionally, this strategy offers premium item versatility and boosted manufacturing speed, therefore boosting total production effectiveness.
Economical Manufacturing Approach
Plastic extrusion jumps to the forefront as an affordable manufacturing method in manufacturing. This procedure stands apart for its capacity to produce high quantities of material quickly and effectively, giving suppliers with significant financial savings. The primary cost benefit is the ability to make use of cheaper resources. Extrusion makes use of Read Full Article thermoplastic products, which are much less expensive contrasted to ceramics or metals. Further, the extrusion process itself is fairly simple, minimizing labor costs. In addition, plastic extrusion requires less power than traditional production methods, contributing to reduced functional expenses. The procedure additionally minimizes waste, as any excess or malfunctioning materials can be reused and reused, supplying an additional layer of cost-effectiveness. On the whole, the monetary advantages make plastic extrusion a highly attractive choice in the manufacturing industry.
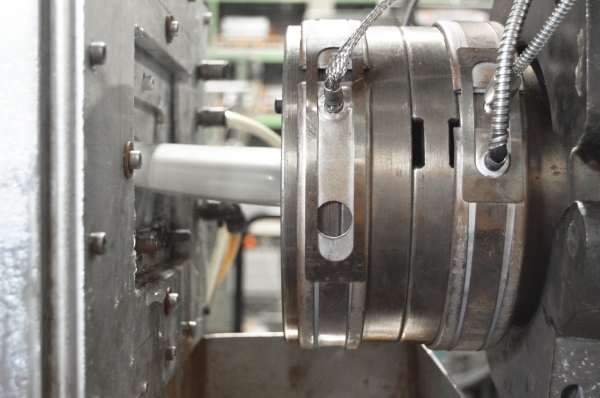
Superior Product Adaptability
Past the cost-effectiveness of plastic extrusion, one more substantial advantage in producing lies in its premium product adaptability. This makes plastic try this site extrusion an optimal remedy for industries that need customized plastic elements, such as vehicle, building and construction, and packaging. In significance, plastic extrusion's product flexibility promotes technology while improving functional efficiency.
Improved Manufacturing Rate
A substantial benefit of plastic extrusion lies in its boosted manufacturing rate. Couple of various other manufacturing processes can match the speed of plastic extrusion. Additionally, the capacity to preserve constant high-speed manufacturing without compromising product top quality sets plastic extrusion apart from various other techniques.
Real-world Applications and Effects of Plastic Extrusion
In the world of production, the technique of plastic extrusion holds profound relevance. The financial benefit of plastic extrusion, mainly its high-volume and cost-effective output, has reinvented manufacturing. The industry is persistently striving for developments in recyclable and biodegradable materials, indicating a future where the benefits of plastic extrusion can be retained without jeopardizing environmental sustainability.
Conclusion
In conclusion, plastic extrusion is a extremely reliable and reliable approach of changing resources into diverse items. It uses many advantages over other plastic forming techniques, including cost-effectiveness, high result, marginal waste, and layout flexibility. Its influence is greatly felt in different markets such as building, automobile, and durable goods, making it a crucial procedure in today's production landscape.
Delving deeper right into the technical process of plastic extrusion, it starts with the selection of the suitable plastic material. When cooled, the plastic is reduced right into the called for lengths or injury onto reels if the product is a plastic film or sheet - plastic extrusion. Comparing Plastic Extrusion to Various Other Plastic Forming Techniques
Understanding the types of plastic suitable for extrusion leads the way for a wider discussion on exactly how plastic extrusion stacks up against various other plastic forming methods. Couple of other production procedures can match the rate of plastic extrusion.